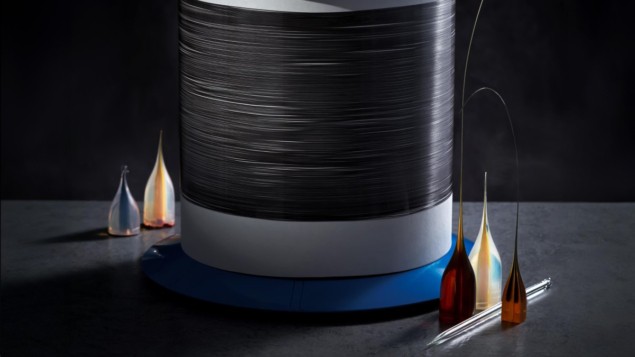
Ultralong, fracture-free semiconductor fibres have been produced inside glass cladding by researchers in Singapore and China. By etching off the glass and replacing it with a flexible polymer sheath embedded with metallic wires, the researchers were able to produce microscale fibres that could be spun into textiles. The work, which builds on a long-standing quest to produce fibre-based electronics, could have applications in smart clothing, medical devices and potentially in photonics.
The first fibres containing a semiconductor inside optical glass were developed by chemist John Badding of the Pennsylvania State University in the US following a sabbatical at the University of Southampton in the UK. He used high-pressure chemical vapour deposition to place various materials inside a hollow-core optical fibre. “[Badding] came to me and said, ‘Is this any good?’ and I was, like, ‘You’re kidding me, this is amazing!’ and we started collaborating,” says materials scientist and engineer Venkatraman Gopalan, also of Penn State. The technique was hamstrung by the slow production rate of the fibres, however, and the collaboration effectively ended after the sudden death of Badding at 57 in 2019.
In 2008 John Ballato of Clemson University in South Carolina developed the molten core method for producing optical fibres of silicon and germanium. The two materials are heated above their melting points of over 1000 °C. The molten silicon is then injected into the glass as it is drawn into a fibre and, as the two cool, one solid surrounds the other. This method allows tens of metres to be produced every minute, and the fibres have attracted interest for medical lasers, nonlinear optics and various other applications. One problem is that differences in the thermal expansion coefficients between the semiconductor and the glass cause the semiconductor to fracture as it cools. This creates optical losses and makes it impossible to remove the glass without the fibre falling apart.
Cracking new study
In the new work, researchers at Nanyang Technological University in Singapore, Jilin University in China and elsewhere conducted a thorough study of this cracking. “We worked with mechanical experts who helped us to explain what the key factors are,” says Lei Wei of Nanyang Technological University. This improved theoretical understanding allowed the researchers to choose aluminosilicate glass to clad germanium, for example. The result was long semiconductor wires encased in glass without the cracks.
In future, the researchers believe these glass-clad fibres could be useful in photonics. In the present paper, however, they etched off the glass to leave the silicon wires less than 100 micron thick. “For electronics, a semiconductor alone will not work, we need to have metal contacts to talk to the semiconductor,” says Wei. They therefore used a low-temperature process to attach two metal wires embedded in a conductive polymer to the semiconductor and embedded the three leads together in an insulating polymer. The result was a flexible optoelectronic fibre that could be spun into a yarn.
The team produced several devices containing their yarn interwoven into other textiles. One example was a beanie hat that could detect the light from a traffic signal and produce a vibratory signal on a mobile phone indicating whether the signal was red or green. This, they envisage, could help a visually impaired person. Another was a smartwatch strap that could measure a person’s heart rhythm.
Washable transistor could be next
They also showed that the technology has a practical resilience. “We put our device into the washing machine…We can wash it multiple times and it still maintains its original performance,” says Lei Wei. The researchers are now attempting to fabricate a transistor inside the fibre to allow more direct incorporation of electronic circuitry.

Optical fibres with integrated semiconductor junctions developed
Ballato is enthusiastic about the research. “I’ve known this group for 15 years, so I’m not surprised by the excellence of the work,” he says; “They’ve been able to take these important but somewhat academic concepts and reduce them to practice in a very useful and important way that validates the scalability of the fibres themselves.”
He is most impressed by the team’s ability to combine materials that require different processing conditions into a single structure. “With this new toolkit, they are ahead of everyone else in the ability to use them to develop practical, functional devices,” he says.
“This is very exciting – John [Badding] would have been thrilled to see this!” says Gopalan. He believes that for sensing and imaging, the technique shows real promise, although he says that the current fibres would be too thick for practical use in signal transmission, and suspects the molten core process might not be able to produce sufficiently pure, thin fibres for signal transmission at all. The next step is “to thoroughly characterize the basic electronic and optical properties of these fibres,” he says: “That will determine where the applications may lie.”
The fabrication process is described in Nature.
- SEO Powered Content & PR Distribution. Get Amplified Today.
- PlatoData.Network Vertical Generative Ai. Empower Yourself. Access Here.
- PlatoAiStream. Web3 Intelligence. Knowledge Amplified. Access Here.
- PlatoESG. Carbon, CleanTech, Energy, Environment, Solar, Waste Management. Access Here.
- PlatoHealth. Biotech and Clinical Trials Intelligence. Access Here.
- Source: https://physicsworld.com/a/semiconductor-fibres-are-fracture-free-and-glass-clad/